Extruded aluminum is a type of metal that is made through a process called extrusion. In extrusion, molten metal is forced through a series of dies to create the desired shape. This process is often used to create lightweight profiles and parts that require a high level of strength and accuracy. Aluminum is an essential metal for many applications because of its strength, lightweight, and corrosion resistance. So if you’re looking for a versatile material that can be used in many different ways, extruded may be the perfect option for you.
Extruded aluminum
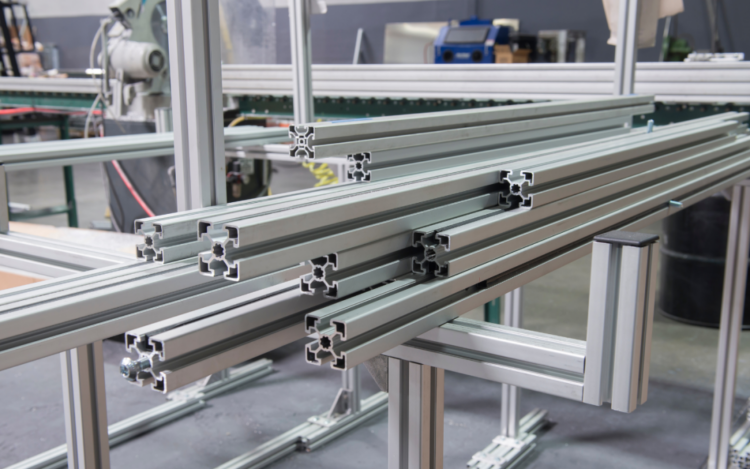
Extruded aluminum is a process by which aluminum alloy material is forced through a die with a specific cross-sectional profile. Aluminum extrusion can be seen as the process of squeezing toothpaste from a tube. When you apply pressure to it, aluminum gets squeezed into a smaller space and emerges from the die opening.
One of the most important differences between extruded and cast is that extruded has greater strength and stiffness than a cast one. This is because it is made from much more uniform materials, which means that there are no areas of weakness or inconsistencies in the metal. They also have a wider range of applications than cast does, which makes them ideal for products that require high durability and resistance to wear and tear.
What are the different types of aluminum?
It is produced in three grades: 1100, 3003, and 6061. The type of aluminum used in a particular design will usually determine the final price point and application. For example, 1100 is made from a cheaper material than 6061, but cannot be used for high-temperature uses.
2024 aluminum extrusions are a more expensive alloy than 3003 extrusions but have good machinability and workability. It also has excellent strength ratings, making it the most suitable for aerospace designs. However, like any other alloy, 2024 has weaknesses. 2024 is prone to corrosion and weakening of the welds. However, these shortfalls do not affect the quality of the product during production.
It is most commonly found in products that require lightweightness and strength, including cars, aircraft, and kitchenware. It is also used in construction materials like roofing tiles and window frames.
What are the different types of extruded aluminum?
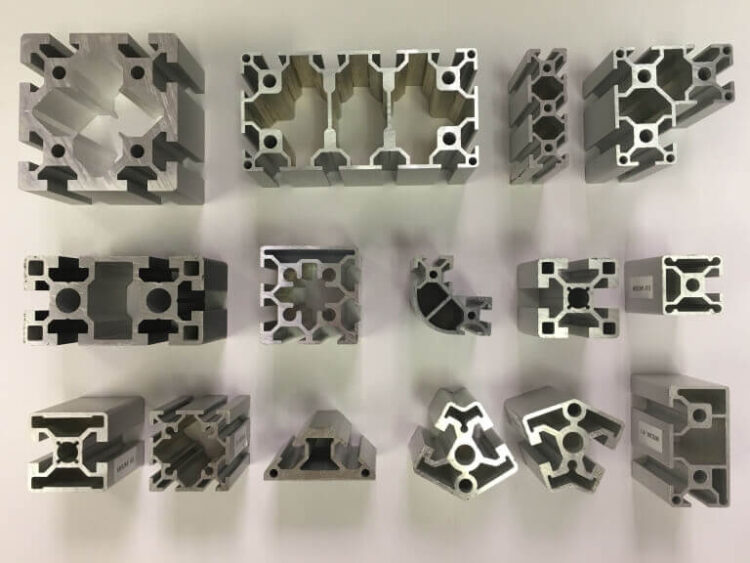
Extruded aluminum is a type of metal that is formed into shapes by being bent or shaped into a specific shape. Aluminum angles are the most common type of extruded part, and they are typically formed into L-shaped parts with two legs that are formed by bending the extrusion to a 90-degree angle. Beams are also commonly made from extruded aluminum, and they are typically created by bending the extrusion into a U-shape.
Channels can be created from extruded aluminum as well, and they usually consist of a series of straight lines that run along the length of the channel. Tubing can also be produced in various different shapes, and these shapes can include things like tubes, circles, and squares. Lastly, extruded aluminum can also be produced in the form of extrusions, which are pieces of metal that have been shaped using an extruder machine.
How many types of extrusion are there?
1. Cold Extrusion
This type of extrusion is used most often to produce dough or pasta. It involves feeding a continuous stream of dough through a die, which cuts the dough into small pieces as it passes by. This process is slow and can be difficult to control, so it’s not used for large objects.
2. Hot extrusion
Hot extrusion uses a force called compression to form profiles with a constant longitudinal cross-section. With a single step, you can manufacture solid or hollow bars with complex geometries and fixed cross-sections that have smooth surfaces. They can be solid or hollow, with a variety of shapes and cross-sections.
3. Friction Extrusion
This type of extrusion is used mostly to make high-quality plastics. It works by forcing hot molten plastic through a die against resistance (usually from an air pressure difference). This process creates smooth edges and consistent sizes because the die never has to deal with chunks of solid plastic.
4. Micro Extrusion
Micro extrusion is unique because it doesn’t involve any dies at all. Instead, tiny nozzles called “microdispersers” shoot streams of molten metal directly toward the object you want to create. Because there’s no need for cutting or shaping, this process is incredibly accurate and fast.
How is extruded aluminum made?
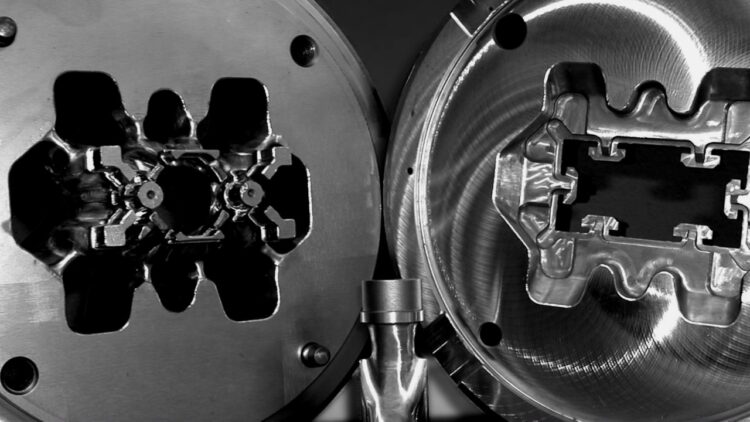
It is a process where aluminum billets are heated and pushed through a shaped die opening. With an opening that can be modified to create different shapes and sizes, they will provide every user with the specific needs they want to fulfill. All aluminum bar types differ, so we must use different steel dies. There are many benefits to extrusion over other manufacturing processes, such as higher strength and stiffness values, better heat treatment properties, and lower production costs.
Extrusion creates an even wall thickness throughout the bar, which results in a stronger product. Additionally, extrusion creates a more consistent color throughout the bar, eliminating the need for finishing processes such as anodizing or powder coating.
Benefits of extruded aluminum
It has many benefits over other types of aluminum, including being lightweight and strong. It is also corrosion-resistant and quick-to-market, making it a great choice for products that need to be quickly shipped or sold. Extruded aluminum is also sustainable because it can be recycled multiple times. Finally, extruded aluminum is an excellent conductor of electricity and heat, making it perfect for applications like wiring and engine parts.
Why is extrusion better than rolling?
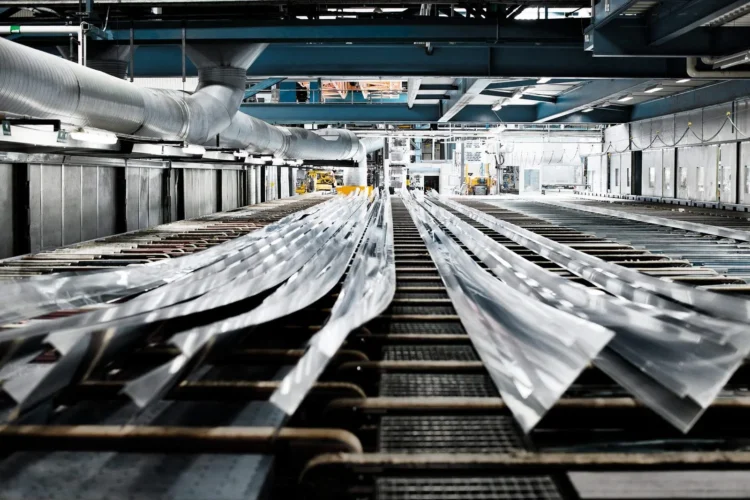
The high pressure and temperature make the metal solidify quickly, which creates the extruded product. This method produces a greater quantity of material than rolling, meaning that extruded products are usually stronger and more durable. All in all, extruded has many advantages over rolled products. However, one of the main advantages of extruded aluminum is that it has greater strength and durability due to the use of more material in the fabrication process.
Conclusion
Whether you are building a new product or just refinishing an existing one, it’s important to understand the difference between aluminum and extruded aluminum. Both materials are used in different applications, but knowing the basics can help you make better decisions when selecting the right material for your project.