In various industries, lifting heavy objects and materials is a common occurrence. To ensure these lifting operations’ safety and efficiency, support solutions such as lifting slings have become crucial. This article will explore the significance of lifting slings and their role in material handling.
1. Understanding the Importance of Lifting Slings
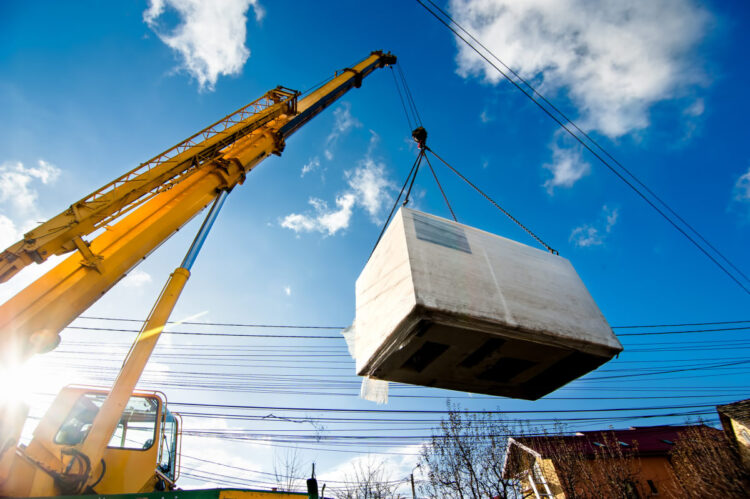
Enhancing Safety During Lifting Operations
Lifting heavy loads without the appropriate equipment can pose significant risks to workers and the lifted materials. Lifting slings play a crucial role in ensuring safety during these operations. By securely holding the load and evenly distributing its weight, slings reduce the chances of accidents such as load shifting or falling.
Boosting Efficiency and Productivity
Efficiency and productivity are paramount in any lifting operation. Lifting slings offer numerous advantages in this regard. Slings enable precise control and maneuverability by providing a secure and stable grip on the load. Workers can lift and transport materials more easily and accurately, saving time.
Versatility
Lifting slings come in different types and configurations, allowing them to adapt to various lifting tasks. Whether it’s wire rope slings for heavy loads, chain slings for harsh environments, webbing slings for delicate materials, or round slings for irregularly shaped loads, having a variety of options enhances the efficiency and flexibility of lifting operations.
Quick and Easy Setup
Lifting slings are designed for easy and fast setup. With proper training and knowledge, workers can efficiently attach the slings to the load and lifting equipment, reducing downtime and maximising productivity.
Time-Saving
Workers can lift and transport materials more easily and accurately using lifting slings. Slings enable precise control and maneuverability, allowing for efficient placement of the load at the desired location. This saves time compared to alternative methods requiring more complex rigging or manual handling.
Increased Safety
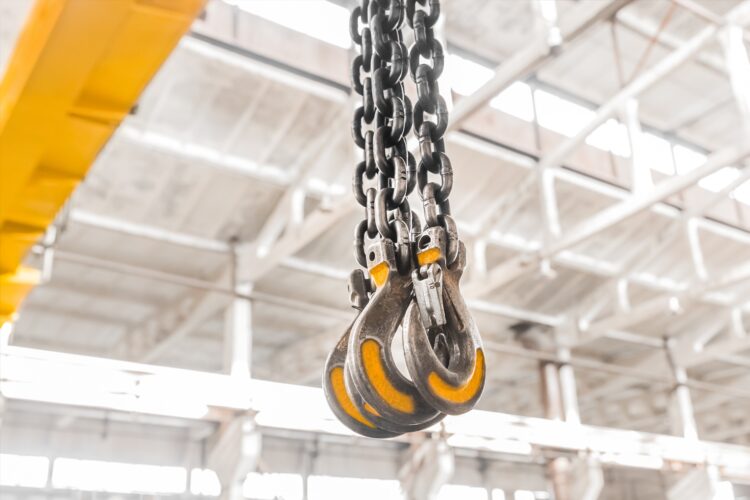
When used correctly, lifting slings enhance safety in lifting operations. They provide a reliable means of securing loads, reducing the risk of accidents and injuries. Workers can confidently focus on their tasks, knowing that the slings are designed to handle the specific load requirements and provide the necessary strength and stability.
Reduced Damage and Downtime
Lifting slings, such as webbing or round slings, are designed to minimise the risk of damage to delicate or polished loads. Workers can use the appropriate sling type to protect the load’s surface and prevent costly damages. This saves money and reduces downtime associated with repairs or replacements.
Durability and Longevity
Lifting slings are engineered to withstand demanding lifting tasks and harsh working conditions. Their robust construction and resistance to wear, abrasion, and environmental factors contribute to their longevity. By investing in high-quality slings, companies can minimise downtime and expenses associated with frequent replacements.
2. Exploring Different Types of Lifting Slings
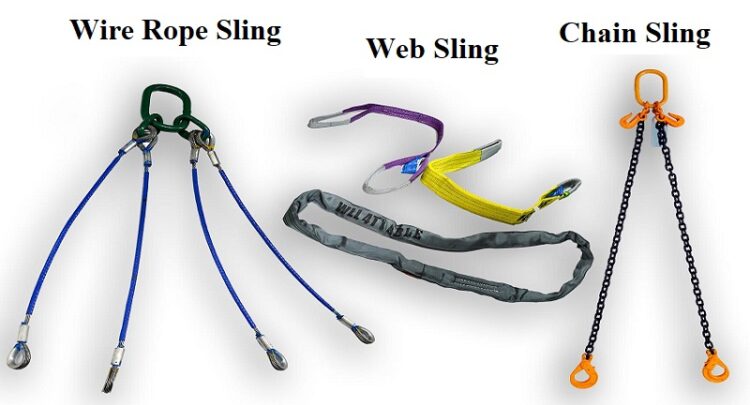
Wire Rope Slings
Wire rope slings are extensively used in heavy-lifting applications. They form strong and flexible slings composed of multiple strands of wire twisted together. Wire rope slings exhibit excellent resistance to abrasion and cutting, making them well-suited for rugged environments. They are often preferred for lifting loads with sharp edges or rough surfaces.
Chain Slings
Chain slings include steel chains and various fittings, such as hooks or shackles. These slings are highly durable and offer exceptional strength. Industries that involve heavy lifting and harsh working conditions commonly utilise chain slings. They provide excellent resistance to heat, chemicals, and UV radiation, making them suitable for various applications.
Webbing Slings
Webbing slings are constructed from woven polyester or nylon material. They are lightweight, flexible, and easy to handle. Webbing slings are ideal for lifting delicate or polished loads, as they minimise the risk of damage. Additionally, they exhibit resistance to mildew, moisture, and most chemicals.
Round Slings
Round slings are soft and flexible slings made of high-strength polyester fibres. They are designed to be gentle on the load’s surface while providing excellent lifting capacity. Round slings are highly adaptable and can lift irregularly shaped or delicate loads.
3. Selecting the Right Lifting Sling for Your Requirements
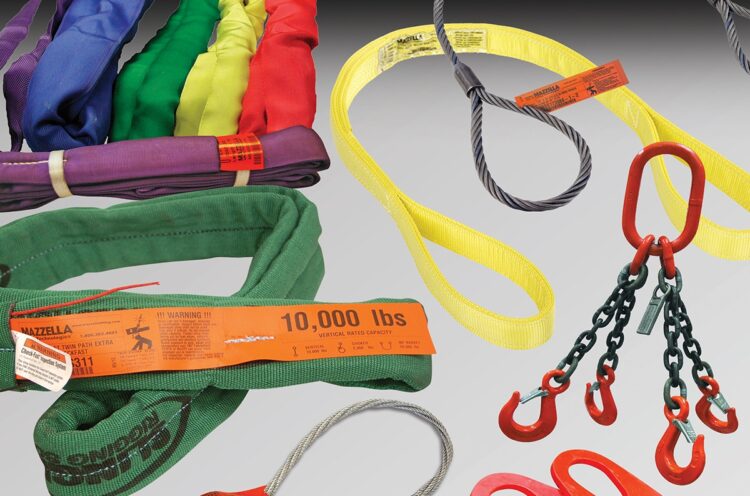
Choosing the appropriate lifting sling ensures safe and efficient material handling. Consider the following factors when selecting a lifting sling:
Evaluating Weight Capacity Considerations
Evaluate the weight of the load and select a lifting sling with an appropriate working load limit (WLL) to safely handle the required weight. Consider both static and dynamic loads encountered during the lifting operation.
Factoring in Environmental Conditions
Different lifting slings have varying levels of resistance to environmental factors. Choose a sling material that can withstand the conditions present in your workplace.
Ensuring Load Protection and Compatibility
Consider the type and shape of the load to be lifted. Certain slings, such as webbing slings, provide better load protection and prevent damage to delicate or polished surfaces. Ensure the lifting sling is compatible with the load’s shape and weight distribution.
4. Proper Usage and Maintenance Guidelines for Lifting Slings
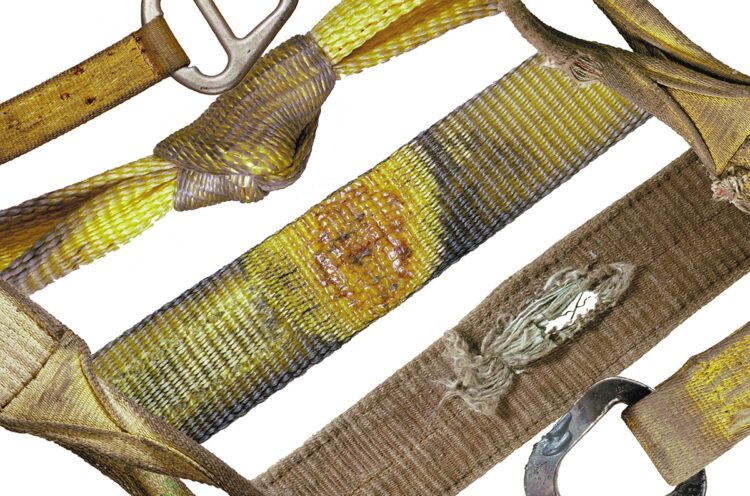
To maximise the lifespan and effectiveness of lifting slings, it is essential to follow proper usage and maintenance guidelines:
Thorough Inspection and Certification
Thorough inspection and certification of lifting slings are crucial to maintaining safety and compliance in lifting operations. To ensure the reliability and integrity of the slings, the following practices should be followed.
Before each use, it is essential to examine the slings thoroughly. This inspection should involve carefully examining the entire length of the sling, including all components such as hooks, fittings, and attachments. Look for any signs of damage, wear, deformation, or corrosion that could compromise the sling’s strength and performance.
Periodic Inspections
Periodic inspections should also be conducted by qualified personnel. These inspections, which are more in-depth than daily examinations, help identify any underlying issues or wear that may not be apparent during routine inspections. The frequency of periodic inspections should align with industry standards and regulations or manufacturer recommendations.
Furthermore, ensuring that the lifting slings meet relevant safety standards and certifications is crucial. This involves sourcing slings from reputable manufacturers that adhere to industry best practices and comply with applicable regulations.
Certified slings undergo rigorous testing to verify their strength, performance, and adherence to safety standards. By using certified slings, you can have confidence in their quality and reliability for lifting operations.
Regular and thorough inspections, both before each use and periodically, help identify any potential risks or issues with the slings. By promptly addressing any concerns and replacing damaged or worn slings, you ensure the safety of workers, prevent accidents, and maintain compliance with safety regulations.
Storage and Handling Best Practices
Proper storage and handling are crucial to prevent damage and maintain the integrity of lifting slings. Store slings in a clean and dry environment, away from direct sunlight and chemicals. Avoid sharp edges or abrasive surfaces that can cause premature wear.
Regular Maintenance and Replacement Procedures
Implement a maintenance program to ensure lifting slings’ ongoing safety and reliability. Replace slings that exhibit signs of wear, damage, or reduced load capacity.
Conclusion
Businesses can enhance workplace safety, improve productivity, and protect valuable assets by selecting the correct lifting slings, considering weight capacity and environmental factors, and adhering to proper usage and maintenance practices. Always prioritise the safety of workers and the materials being lifted.