Valves, those inconspicuous devices responsible for regulating fluid flow, pressure, and direction, play an indispensable role in our daily lives. Whether it’s the tap water we rely on for hydration or the liquefied petroleum gas stove we use for cooking, valves are the unsung heroes working behind the scenes. These remarkable contraptions, comprised of various components like bodies, covers, valve seats, opening and closing mechanisms, driving systems, and connectors, have a rich history and a pervasive presence in mechanical machinery, from engines to ships. Let’s embark on a journey to uncover the evolution and significance of valves, those unsung champions of fluid control!
Historical background
The origins of valves trace back to ancient China, where bamboo pipes and cork valves were employed in water piping systems and irrigation canals. As smelting technology and hydraulic machinery reached Europe, ingenious lead and copper cock valves emerged, revolutionizing the way fluids were managed. In the late 17th century the lever safety valve was born, designed specifically for boilers. However, it was the advent of the steam engine in the 18th century that truly propelled valves into the mechanical industry. Plug valves, safety valves, and butterfly valves took center stage, effectively controlling the flow of steam. But as steam flow and pressure increased, traditional stopcocks could no longer meet the demands, leading to the birth of the modern valve.
The ever-evolving design of valves
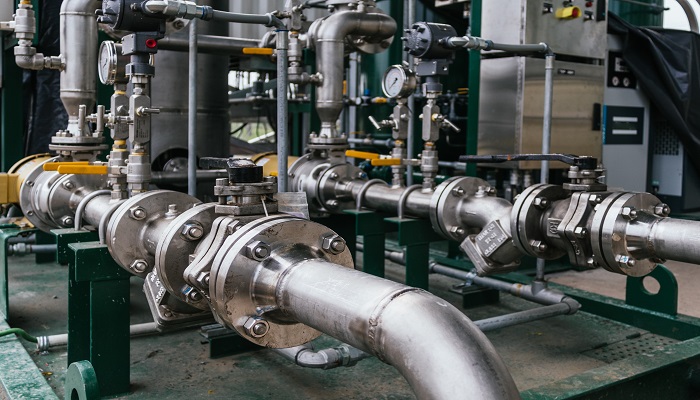
With the dawn of the 19th century, valve production witnessed significant breakthroughs. Threaded stem shut-off valves and wedge gate valves, offering enhanced pressure and temperature capabilities, revolutionized the industry. These advancements not only met the ever-growing demands of diverse sectors but also paved the way for improved flow control. As industries such as electrical power, petroleum, chemicals, and shipbuilding burgeoned, high and medium-pressure valves evolved rapidly, catering to the specific requirements of each domain.
The aftermath of World War II witnessed a valve renaissance, fueled by the development of novel materials like polymers, stainless steel, lubricating substances, and cobalt-based cemented carbide. This breakthrough allowed for the rapid evolution of ball valves and diaphragm valves, setting new benchmarks for efficiency. Meanwhile, globe valves, gate valves, and other valve variants underwent significant improvements, all in pursuit of optimal performance. The valve manufacturing industry emerged as a pivotal force within the machine industry, contributing to remarkable advancements.
The many different types of valves
Valves can be classified into several distinct categories, each serving a unique purpose. These are some of the most common types of valves used in various industries:
1. Gate valve
Gate valves have been in use for centuries, with the oldest known design dating back to ancient Egypt. They are widely used in applications where full flow or isolation is needed, such as in water treatment plants, power plants, and oil refineries. Their slow operation and susceptibility to corrosion can sometimes limit their usage in certain industries.
2. Ball valve
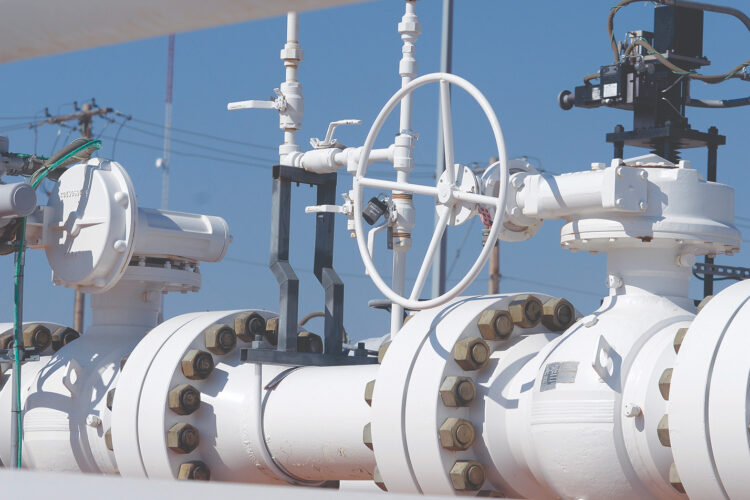
Ball valves were invented in the 1950s and quickly gained popularity due to their reliability and ease of operation. They are commonly used in applications where quick shutoff and tight sealing are required, such as in water supply systems, oil and gas pipelines and industrial processes.
3. Swing check valve
Swing check valves have a long history and have been used in various forms since ancient times. They are essential for preventing backflow and protecting equipment. Swing check valves find applications in numerous industries, including water and wastewater systems, oil and gas pipelines, and HVAC systems.
4. Globe valve
Globe valves have been around for over a century and are known for their precise control over flow rate. They are commonly used in industries requiring accurate throttling, such as in HVAC systems, steam systems, and chemical processing plants.
5. Butterfly valve
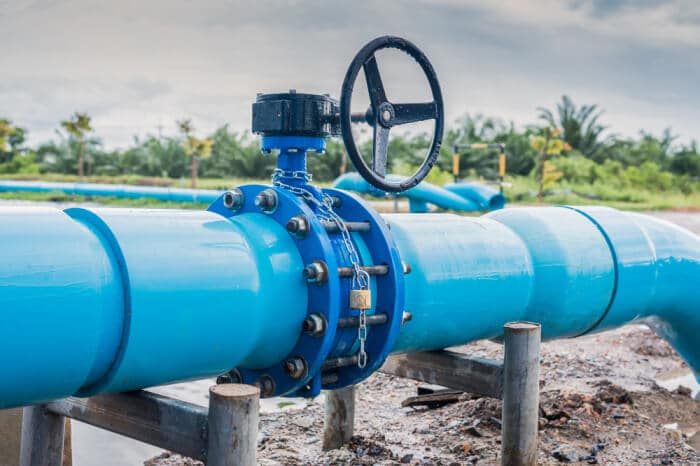
Butterfly valves have been used since the 1930s and gained popularity due to their lightweight construction and cost-effectiveness. They are commonly used in large-diameter applications, such as water distribution networks, sewage systems, and power plants, where quick shutoff and low-pressure drop are important.
6. Diaphragm valve
Diaphragm valves were developed in the 1920s and gained popularity for their ability to handle corrosive fluids and slurries. They are commonly used in industries such as pharmaceuticals, food and beverage, and water treatment, where contamination control and precise flow regulation are critical.
7. Plug valve
Plug valves have been in use for over a century and have evolved to offer improved sealing and durability. They are commonly used in industries such as oil and gas, petrochemicals and wastewater treatment. Plug valves are well-suited for applications where frequent operation and tight sealing are required.
8. Needle valve
Needle valves have been in use for many years and are widely utilized in industries that require precise flow control, such as laboratories, instrumentation systems and hydraulic systems. Their fine-threaded stem allows for gradual adjustments, making them ideal for low-flow applications.
9. Pressure relief valve
The concept of pressure relief valves has been around for centuries, but their modern design and usage have evolved over time. They are crucial safety devices used in various industries, including oil and gas, chemical processing and steam systems, to prevent equipment damage and ensure system integrity during overpressure events.
10. Solenoid valve
Solenoid valves were developed in the early 20th century and gained popularity with the advancement of electrical control systems. They are commonly used in automation and fluid control applications, such as irrigation systems, refrigeration systems, and industrial machinery, where remote operation and quick response are desired.
Modern advancements in valve technology
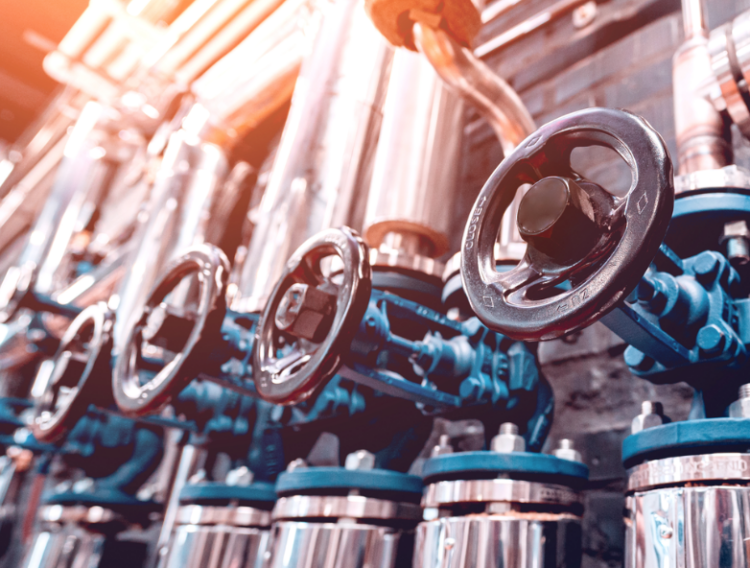
In the modern era, valves have continued to evolve to meet the ever-expanding demands of diverse industries. Valves are now categorized based on nominal pressure, operating temperature, and driving mechanism. From vacuum valves to ultra-high-pressure valves, from standard temperature valves to high-temperature valves, manufacturers have designed valves to meet specific operational requirements. Materials play a vital role, with various metals like cast iron, cast copper, steel, alloys, and stainless steel being selected based on factors such as fluid characteristics, pressure, and temperature. Advancements in polymer technology have also resulted in the extensive use of plastics in valves, offering superior performance and resilience.
Future valve development
Looking ahead, the valve industry continues to push the boundaries of innovation. Efforts are underway to broaden product specifications, introducing energy-saving, labor-saving, and self-control valves. Systems will be upgraded, incorporating new technologies and methods to enhance valve longevity. Specialized valves, including those designed for liquid oxygen, cryogenic fluids, vacuum applications, nuclear environments, and safety measures, will most likely become more prevalent. The future promises exciting developments in valve automation and remote control, as well as program-controlled systems.
Final words
Valves, those unassuming devices silently regulating fluid flows, have an incredible impact on our lives whether we are aware of it or not. From the humble origins of bamboo pipes and cork valves to the advanced materials and technologies of the present, valves have transformed into indispensable components of machinery and infrastructure and have defined our modern society. So the next time you pour yourself a glass of water take a moment to acknowledge and appreciate the ingenuity and versatility of valves, the unsung heroes silently facilitating the smooth operation of countless processes, always ensuring safety, efficiency, and control in the vast world of fluid dynamics, as they keep working hard to ensure the modern world as we know it keeps functioning smoothly!