Urethane casting, a versatile and cost-effective manufacturing process, allows the creation of high-quality prototypes, functional parts, and intricate designs.
However, achieving optimal urethane cast parts requires meticulous attention to several design considerations. This article delves into five essential design tips for precise and durable urethane cast parts.
1. Give Even Wall Thickness
Maintaining uniform wall thickness throughout the urethane casting process is crucial for preventing defects like warping, distortion, or uneven curing. Variations in wall thickness lead to non-uniform heat distribution during the curing process, resulting in stress concentration. This can compromise the part’s structural integrity.
To ensure even thickness, employ design tools and simulation software to analyze flow patterns and optimize gating and venting locations. Aim for wall thicknesses of at least 0.030 inches (0.76mm) for small parts and 0.060 inches (1.52mm) for larger parts.
2. Account for Shrinkage
During the curing process of urethane materials, shrinkage is an inherent phenomenon that must be carefully managed to ensure the dimensional accuracy and fit of cast parts. Shrinkage occurs as the material undergoes polymerization and cross-linking, causing it to contract in volume. The degree of shrinkagein vacuum casting can be influenced by factors such as the specific formulation of the urethane material, the curing temperature, and the curing time.
Different types of urethane materials, such as polyurethane and silicone-based urethanes, may exhibit varying shrinkage rates. For instance, flexible urethane materials tend to exhibit higher shrinkage compared to rigid ones due to differences in their chemical compositions and cross-linking behaviour. It’s essential to consult the manufacturer’s technical data sheets for accurate information on the shrinkage rates of the specific materials you intend to use.
One approach to mitigate the effects of shrinkage is to oversize the original pattern. By intentionally designing the master pattern slightly larger than the desired final dimensions, the anticipated shrinkage can be accounted for, resulting in a correctly sized final part. Another method involves incorporating post-curing steps into the manufacturing process. Post-curing involves subjecting the cast urethane parts to elevated temperatures for an extended period. This additional curing phase encourages further polymerization and cross-linking, reducing residual shrinkage and improving dimensional stability.
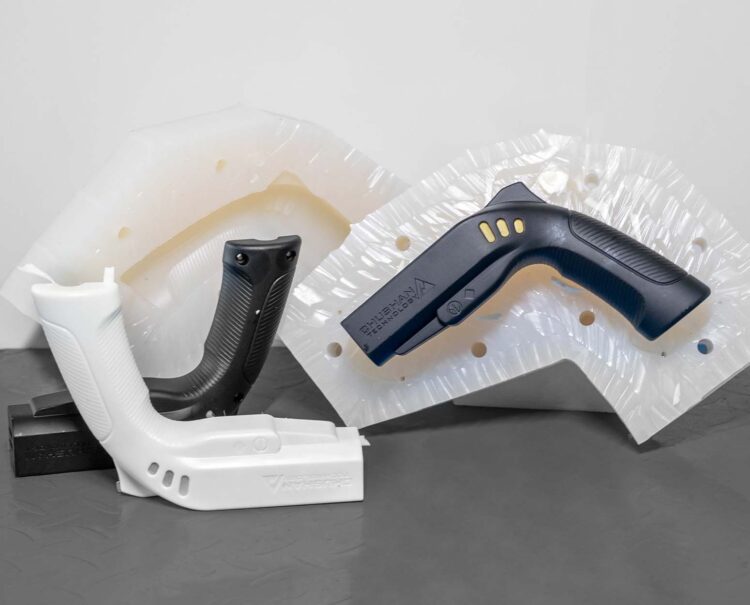
3. Employ Ribs
In the realm of urethane casting, the incorporation of ribs is a fundamental strategy to elevate the structural integrity and resilience of cast parts. Ribs are essentially thin, wall-like structures that intersect the main walls of the part at perpendicular angles. While their primary purpose is stress distribution, the engineering of ribs delves into intricate considerations to ensure optimal urethane casting process.
1. Rib Thickness Optimization
One of the critical factors in rib design is the selection of an appropriate rib thickness. Ideally, rib thickness should fall within the range of 60-70% of the main wall thickness. This balance between rigidity and flexibility is pivotal. Excessive rib thickness can lead to internal stress concentration during curing, causing deformation or part failurein urethane casting process.
On the other hand, overly thin ribs might not effectively distribute stress, negating their purpose. Thus, meticulous calculation and consideration of the material’s mechanical properties, such as modulus of elasticity and elongation, are essential for an informed rib thickness decision.
2. Rib Spacing and Stress Distribution
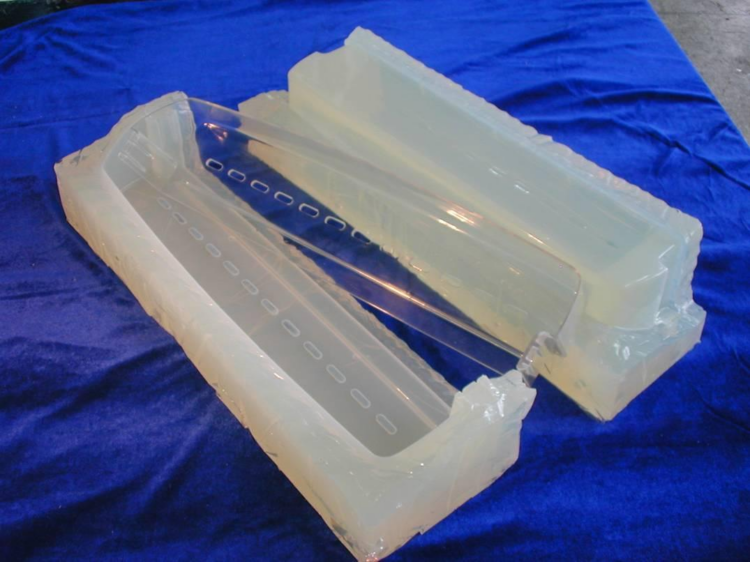
In vacuum casting service Rib spacing plays a crucial role in effective stress distribution and prevention of warping. Optimal rib spacing usually lies between 1.5 to 2 times the rib thickness. Deviations from this range can lead to uneven stress distribution, rendering some areas more susceptible to deformation than others.
Moreover, the relationship between rib spacing and the part’s overall geometry should be considered. Irregular geometries might necessitate variations in rib spacing to maintain consistent mechanical performance.
3. Geometric Considerations
Ribs are not a one-size-fits-all solution; their design is heavily influenced by the part’s geometry. Areas of high-stress concentration, such as corners or load-bearing sections, might require denser rib patterns to reinforce these vulnerable regions. Additionally, rib termination points, where they intersect with other features or walls, should be meticulously designed to prevent stress concentration at these junctions.
4. Consider Drafts and Undercuts
Incorporating appropriate draft angles and addressing potential undercuts in urethane casting designs are critical steps to ensure successful mold release and part quality. Draft angles are inclined surfaces added to the vertical walls of a part to facilitate its easy removal from the mold without causing damage or distortion. The choice of the draft angle depends on factors such as the specific urethane material being used, the complexity of the part’s geometry, and the desired surface finish.
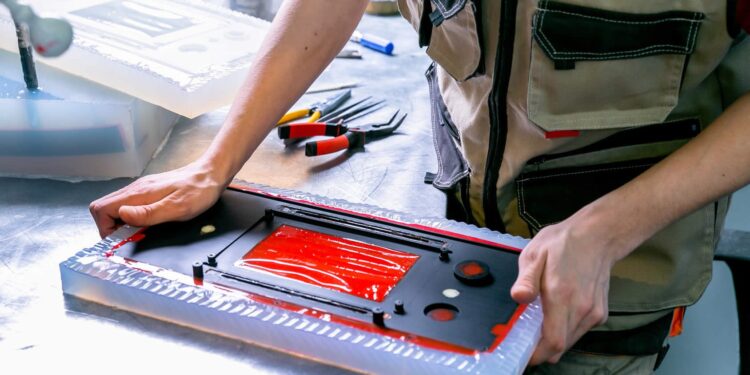
Different urethane materials exhibit varying characteristics in terms of flexibility, hardness, and shrinkage rates. Soft and flexible urethanes may require larger draft angles to allow for their greater elasticity during ejection. For instance, elastomeric urethanes with a lower Shore hardness would benefit from draft angles ranging from 5 to 10 degrees, while harder urethanes could work well with draft angles as low as 1 to 3 degrees. These angles prevent part interference with the mold’s sidewalls during ejection, minimizing friction and reducing the chances of surface imperfections.
Beyond draft angles, assessing and addressing potential undercuts is essential. Undercuts are features in the part design that prevent straightforward ejection from the mold. Incorporating side actions, sliders, or collapsible cores in the mold design can eliminate undercuts. For example, complex geometries like threaded holes, snap fits, or interlocking parts may require advanced mold design techniques to accommodate these features without hindering part removal in vacuum casting.
5. Include Enough Spacing Between Letters and Logos
When incorporating intricate details like text or logos, provide adequate spacing and ensure a minimum height and width for these features. Insufficient spacing can lead to the merging or incomplete formation of these elements. Aim for a minimum of 0.040 inches (1.02mm) in width and depth for legible text and logo details. This helps maintain the integrity of the design during the urethane casting process.
Conclusion
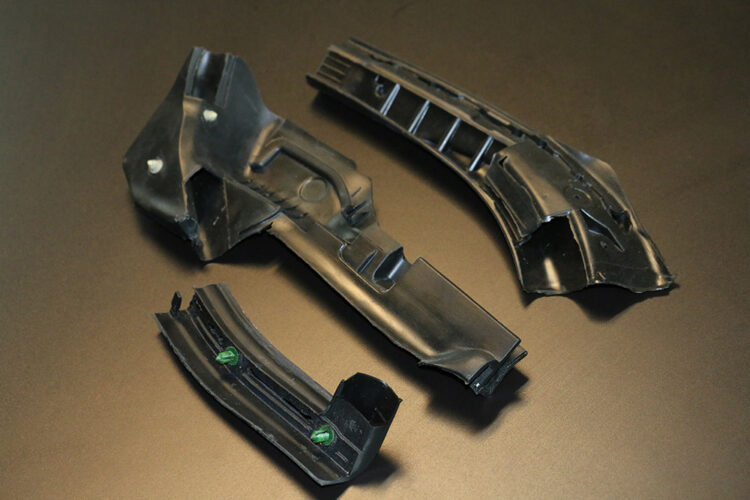
In the realm of urethane casting process, attention to design details is paramount for successful outcomes. Each tip discussed—uniform wall thickness, shrinkage compensation, rib utilization, draft angles, and appropriate spacing—plays a critical role in achieving high-quality cast parts.
By applying these parameters and avoiding pitfalls, manufacturers can produce flawless parts that fulfill functional and aesthetic requirements. Meticulous planning and adherence to these guidelines are the cornerstones of effective urethane casting, leading to prototypes and products of exceptional quality and durability.