Welcome to our blog! We’re here today to answer all your questions about the manufacturing process of sheet metal. It can be a complex process, so we’ve gathered some tips that can help you gain a better understanding. So, buckle up and let’s get into it!
Types of Sheet Metal Manufacturing
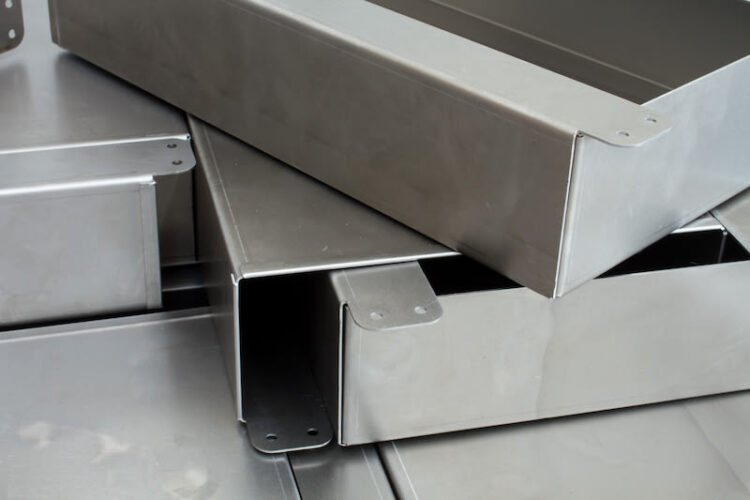
Sheet metal manufacturing is a process that involves the use of a number of different tools and processes to roll, cut, and shape flat pieces of metal into a variety of products. Different types of sheet metal manufacturing are used to create components for a broad range of industries.
These manufacturing processes involve different materials, tools, and techniques. The three main types of sheet metal manufacturing are bending, forming, and welding.
- Bending: The bending process involves the installation of special machines with tooling that enables the operator to use pressure or force to bend the material. It is often used in applications such as creating brackets, braces and all types of frames that require more than one dimension. Bending is one way that specialized parts can be created efficiently with limited resources.
- Forming: It utilizes different tools such as punches and die sets in order to shape material into specific shapes like cylinders or channels. This type of manufacturing is often used for complex designs in order to create three-dimensional shapes from the original flat piece of material. Forming can also be used for low volume production runs when molds would not be cost effective or sufficiently accurate.
- Welding: Welding is one type of sheet metal fabrication which uses heat or pressure to join two pieces together by melting them together at their interface points without melting away the original shape or size. This process produces extremely strong seams between two adjoining metals with minimal distortion in both strength characteristics and tolerances ensure quality along with high physical property values so components created this way are very durable over time even under constant strain and pressure while maintaining optimal levels performance throughout their lifetime usage.
Benefits of Sheet Metal Manufacturing
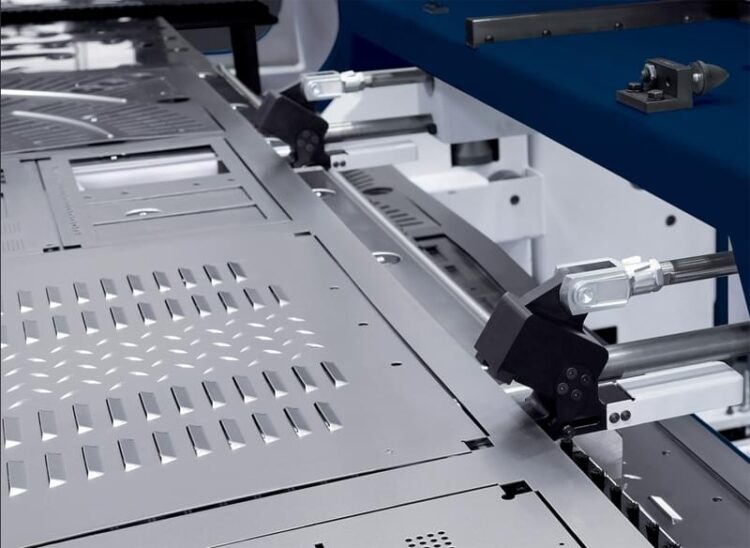
Besides the satisfaction that customers demand from quality products, there are economic benefits as well. Detailed parts can be created with minimum setup since most processes take place within a single working environment, reducing labor costs and cutting lead times. This expedited process allows fabricators to quickly become market differentiators by providing up-to-date products manufactured to exact specifications within weeks rather than months or years.
The strength found in metals is another major benefit, as they can withstand high levels of stress while maintaining their shape and light weight. Sheet metal provides flexibility and durability with uniformity, making it perfect for any application where the structure must remain intact under pressure and weather conditions that could degrade other materials over time. Additionally, manufacturing processes such as electroplating can add additional protections for corrosion resistance or an aesthetically pleasing finish through anodizing or powder coating.
Tools and Equipment Used in Sheet Metal Manufacturing
It involves the shaping of it into components and parts that can then be used for a range of industrial applications. The process is done by taking a large piece of sheet metal, cutting and forming it into the desired shape, and applying finishing touches to the finished product.
Tools and equipment used in the manufacturing process include:
- Shears, press brakes, punches, dies, lasers or water jets to cut panels to size or shape them as required.
- Bending brakes are used to bend the metal at certain angles for smooth curves.
- Rollers also help shape metals by rolling them into different sizes.
- Forge machines are used to create depth in flat surfaces such as embossing or adding texture.
- Mechanical fastening tools may also be needed including rivet guns and welders for joining multiple pieces together.
- Finishing tools including grinders, sanders, polishers and chemical treatments can also be employed to give parts their desired appearance.
Tips for Understanding the Manufacturing Process of Sheet Metal
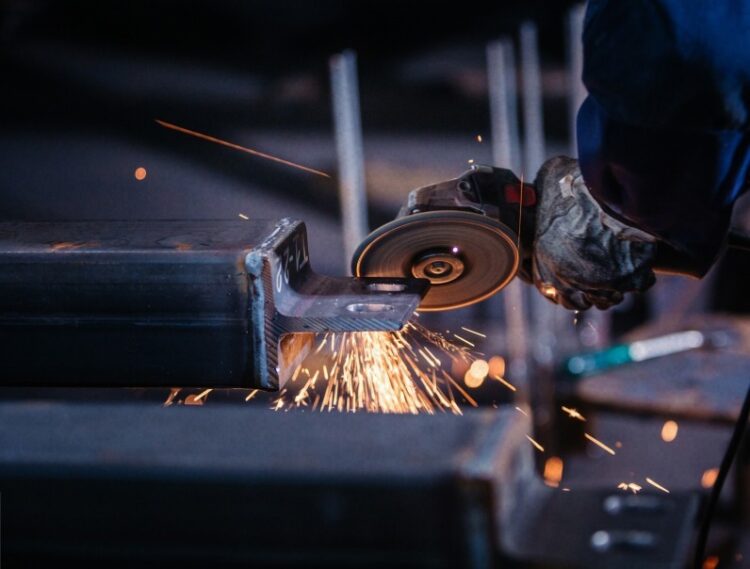
The process often involves a variety of operations including cutting, bending, and forming. Sheet metal is an extremely versatile and popular material used by a wide range of industries to create components and products. However, understanding the steps involved in fabricating sheet metal can be difficult for beginner engineers. This article provides helpful tips that can help you comprehend the intricacies of the sheet metal manufacturing process so you can create products more quickly without running into problems.
- Understand the Methods: Different methods are used for producing sheet materials such as punching, shearing or laser cutting. A good understanding of each technique can speed up your production significantly.
- Know Your Materials: Having an understanding of what materials are suitable for different fabrication processes is important in order to choose the best material for your project. Certain properties such as strength and ductility must be considered according to application requirements when selecting your material.
- Check Thickness Accurately: When selecting a material gauge (thickness) for your project check the thickness range to ensure it suits your requirements.Also remember that thicker materials are usually more expensive than thinner ones, so consider keeping material costs low wherever possible.
- Background Information on Equipment: Making sure you’re familiar with each piece of equipment and its capabilities prior to starting will help speed up production time significantly during fabrication processes like CNC machining and bending operations.
- Focus On Quality Assurance: Quality assurance takes time but makes sure that everything runs smoothly during installation and after use without fail – this includes checking all measurements at every stage of production as well as adhering to customer specifications throughout manufacture, assembly and installation activities.
Conclusion
It is evident that sheet metal products have become essential in a wide range of industries, and particularly in the manufacturing industry. Understanding the diverse processes involved in the manufacture of sheet metal products is therefore paramount.
From knowing how to measure and cut parts to forming and welding them, having an understanding of each step in the process allows teams to create high-quality products efficiently and cost-effectively.
Having a robust understanding of each step helps teams to improve productivity, address quality issues more quickly, reduce waste, and monitor stock levels better. Companies should consider investing in personnel training on the manufacturing process of sheet metal so that they can maximize their resources as well as their profits.