Investment casting is an age-old technique that has allowed us to craft intricate shapes out of metal for centuries! From swords in ancient times to modern car parts, investment casting has allowed us to create complex parts with remarkable detail.
In this blog post, we’ll explore the basics of this fascinating process and take a deeper look at what it takes to make an investment casting. So, grab a cup of coffee and let’s get started!
Benefits of Investment Casting
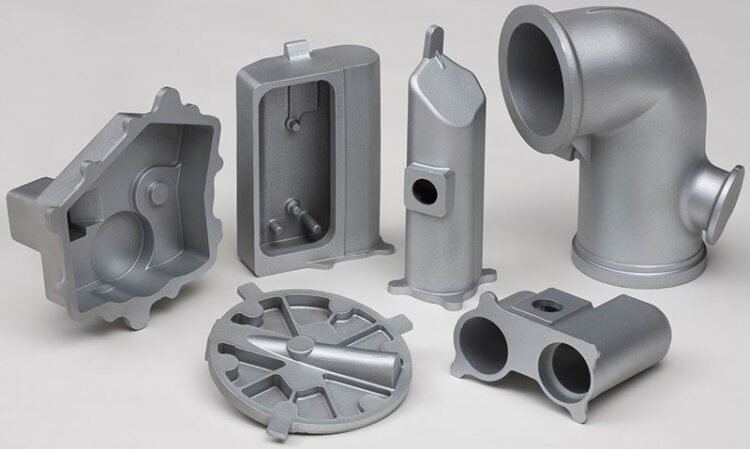
Investment casting process is an established manufacturing process that provides numerous benefits to businesses in comparison to other casting methods. Investment casting yields components with better dimensional accuracy and complex geometries than sand or die-castings. In addition, it allows for greater range of material selection featuring both ferrous and non-ferrous alloys, plus improves finishes in terms of smoothness and texture in the final product.
It is also capable of producing intricate castings with thin walls which can offer weight savings compared to traditional processes. These combined advantages result in lower manufacturing costs, while the improved quality increases the durability and reliability of a wide variety of components.
Investment Casting Process Overview
It is a multi-step procedure for producing custom, high-precision metal parts. This manufacturing technique dates back to ancient civilization and has been used throughout the centuries in different forms. The modern investment casting process is used for creating complex shapes with precise detail, and offers many advantages over other production methods. The following outlines the basic steps involved in this process:
- Creation of Pattern: A wax pattern must be created in the desired shape of the part. This pattern can be produced through several processes, such as injection molding or 3D printing.
- Coating: The wax pattern is dipped into a slurry mixture containing ceramic material and then dried in a furnace to form a rigid coating around it (shell). The wax pattern is then melted away, leaving an impression inside the hard shell (investment).
- Firing: The shell-encased investment is baked at very high temperatures to remove all remaining wax and give it its strength and rigidity. It is then placed into an oven at even higher temperatures so that molten metal such as steel or stainless steel can be poured into the cavity created by the lost wax pattern during step 2. This step completes the molding process for creation of part from molten material.
- Finishing & Machining: After cooling, any extra material needs to be removed from around the part’s surface by machining or grinding processes like CNC turning or need to do some finishing work like polishing for aesthetics if required. At this point, you will have your completed unique component ready for use!
Pattern Making
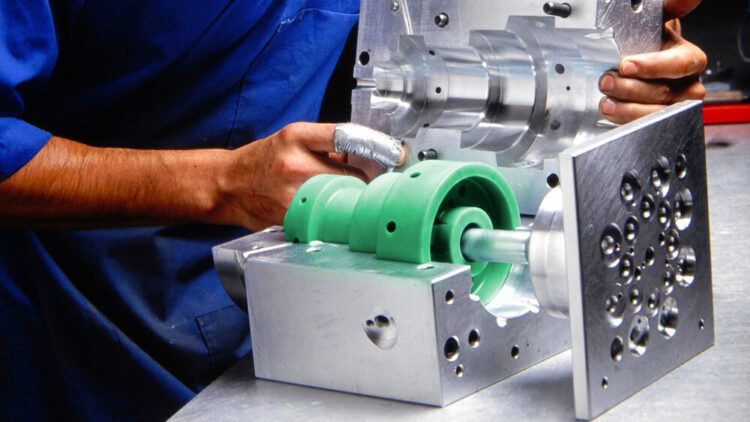
Pattern making makes up the first step of this process. After consulting with the customer to ensure that all design and material specs are in order, a pattern is created for each individual part or group of pieces that needs to be cast. These patterns are typically made out of wood, plastic or wax. If wax is used, it should be slightly softer than the casting alloy so it can easily be removed from the mold with minimal damage to its shape and detail level.
Once all patterns have been created and inspected to make sure they meet necessary specifications, they are attached to a tree-like assembly called a “gating system” that feeds molten metal into the cavity left by the lost pattern during pouring.
Wax Injection
Wax Injection is the next step in the investment casting process. Pre-made waxis injected into a metal die creating a replica of the desired part. The injection process produces hundreds or even thousands of identical wax patterns with high dimensional accuracy.
After injection, the wax patterns are typically sprued up and burnt off in preparation for casting. Sprue connections provide molten metal as an entry point when poured, and often connecting multiple patterns enhances the effectiveness of this step.
Depending on the application, several techniques are used to connect components. These techniques often involve:
- Joining multiple parts to form a single mold
- Creating sprues from predetermined assembly points on each pattern.
Shell Building
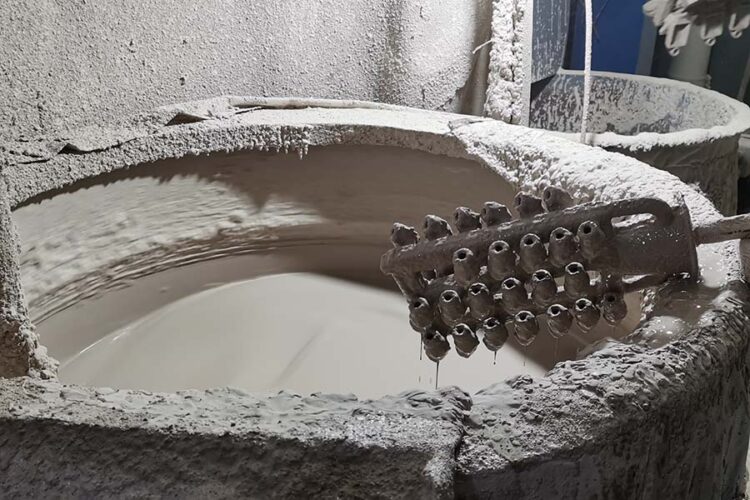
It is a multi-step process that typically starts with the initial wax pattern. This wax pattern closely resembles the desired end product’s design. A metal frame, known as a “tree,” is then built around the wax pattern. In this tree, each branch will have several wax patterns sprouting from it as if it were a tree covered with fruit. The number of branches and wax patterns correlates to how many parts will be produced from this one tree during the final casting process.
Next, several ceramic refractory materials are used to build up multiple layers to create an exterior shell for each piece on the tree. Traditional materials include silica sand and clays mixed with water and organic binders like mullite stucco or alumina hydrate stucco. Each slurry layer must be dried in-between applications to allow for proper curing and green strength of each layer before additional layers can be applied on top of it until reaching desired dimensions and rigidity of shell walls.
Thickness of shells built depends upon part geometry being cast by allowing for amounts elimination during dewaxing process along with shrink allowances determined by material to be cast. As there are many factors that play into successful shell building processes, having an experienced team in place familiar with these variables will help ensure surface cosmetic reproduction accuracy and integrity along with achieved tolerances when manufacturing parts using investment casting processes.
Casting and Finishing
Casting and Finishing: After the mold is prepared with cores and the molten metal is poured in, a finished shape with detailed features is created. The cast part must then undergo various heat treatments and finishing operations. The appearance of the casting can be improved by applying surface treatments, such as painting or coating, which also provides additional protection against wear and corrosion. Machining operations may also be used to enhance dimensional accuracy and improve surface finish.